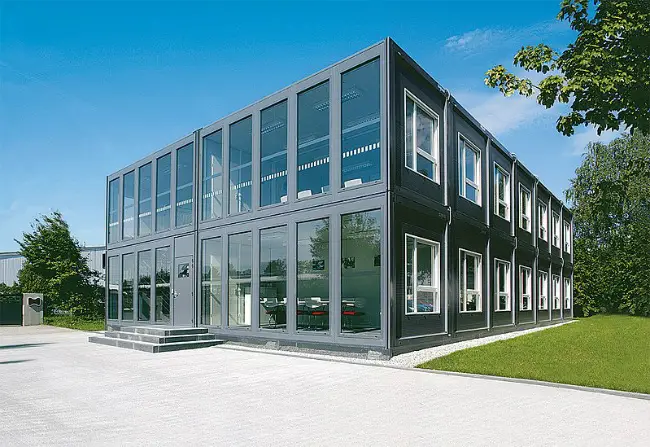
Modular buildings have become an increasingly popular choice for many construction projects in recent years. As opposed to traditional buildings constructed entirely on-site, modular buildings are manufactured off-site in sections, or modules, and then transported to the final location for assembly.
One of the key considerations when opting for a modular building is its intended lifespan. Modular construction offers many advantages, but how long can a modular building be expected to last compared to conventional buildings?
Typical Lifespan
Most modular buildings are designed for a lifespan of at least 50 years. With the right maintenance, a modular structure can have an indefinite service life, especially if the building has been created using durable materials.
Buildings classified as temporary or relocatable modular structures tend to have shorter lifespans, from around 10-30 years. However permanent modular buildings used for long-term, ongoing purposes are generally built to last many decades.
Properly designed and assembled modular buildings have a similar expected lifespan to conventionally constructed buildings. Any differential is down to the materials used and the quality of the building process, not the fact it is modular.
Many companies would prefer not to buy a new portable cabin / modular building and instead opt for used cabin sales, in which case the history of the building needs to be considered. There are, of course, other influencing factors that you should consider.
Influencing Factors
There are several key factors that influence how long a modular building will last:
- Building purpose – Temporary structures have a shorter anticipated life than permanent buildings designed for long-term use.
- Materials used – Durability is affected by the quality of materials such as steel, concrete, and cladding used to protect the building’s exterior.
- Maintenance – Regular upkeep and repair work is essential to achieve maximum lifespan.
- Location – Environmental factors like weather conditions impact on wear and tear over time.
- Quality of build – Precision manufacturing and high-quality assembly supports longevity.
By optimising these factors, a modular building can achieve a lifespan as long as any comparable traditionally built structure.
Materials
The materials used play a major role in determining modular building lifespan. Modular construction relies on precision prefabrication of sections using different materials:
- Steel – The underlying steel structural frame must be appropriately treated to handle corrosion. Hot-dip galvanising is preferable for long-term durability.
- Concrete – Pre-cast concrete panels for walls and floors also need to be made of dense, high-quality concrete to avoid deterioration.
- Timber – Treated timber that is well-maintained can last for decades. Laminated veneer lumber offers the best longevity.
- Cladding – Metal cladding or brick finishes boost lifespan compared to cheaper plastic alternatives.
Using proven durable materials – though more expensive – leads to buildings that can endure for 60+ years with proper care.
Maintenance
No building will achieve its expected lifespan without appropriate maintenance and repairs over time. Modular buildings are the same. Key maintenance factors include:
- Weatherproofing – Checking seals and repairing any leaks quickly is crucial to limit water damage.
- Corrosion – Look out for corrosion of steel parts and treat accordingly to avoid further deterioration.
- Timber care – Regular treatment of exposed timber, along with painting/varnishing, will extend its life.
- Cleaning – Removing dirt, grime and vegetation from the structure prevents premature wear.
- Inspections – Annual inspections identify any issues early so they can be fixed before major problems arise.
With detailed maintenance procedures in place, a modular building will easily reach its anticipated lifespan.
Location Impacts
The location and environment of the modular building will influence its rate of wear and tear. Relevant factors include:
- Weather – Exposure to extreme weather causes faster deterioration. Hot, humid, coastal and cold climates are harshest.
- Pollution – Industrial or urban settings involve higher pollution affecting external surfaces.
- Use – More foot traffic and activity causes greater wear than occasional access.
- Landscape – Positioning on flat, even ground reduces stresses compared to sloped sites.
- Drainage – Good drainage and runoff helps limit water damage.
Optimising location or providing protection against the elements will help maximise lifespan.
Quality of Construction
A core benefit of modular construction is the precision and quality control enabled by factory manufacturing. This leads to buildings with high structural integrity when assembled on-site.
Signs of quality construction include:
- Precision fabrication – Components fit together accurately thanks to computer-controlled manufacturing.
- Quality control – Production in a controlled factory environment results in robust structures.
- Effective sealing – Superior seals properly connect modules, preventing moisture ingress.
- Secure connections – Robust integrations of modules and components create stable structures.
- Foundation design – Good on-site preparation and integration with foundations prevents subsidence.
Durability and longevity are built-in through the modular construction process, rather than relying solely on on-site building skills.
Design Life of Components
When designing a modular building for longevity, engineers will specify certain expected minimum design lives for different components:
- Structure – 60+ years
- Foundations – 60 years
- Roof – 30-60 years
- External walls – 60+ years
- Windows – 25 years
- Doors – 30 years
- Internal fittings – 10-20 years
- Decorative finishes – 25 years
So while the overall building lifecycle may be 60+ years, some internal components and finishes may require replacement over that period. This is normal, as also seen in traditional buildings.
Relocatable Buildings
Relocatable modular buildings are designed to be dismantled, transported and reconstructed if needed. This obviously limits their anticipated lifespan compared to permanent structures.
Typical service life expectancies for relocatable buildings are:
- Site cabins – 5-10 years
- Classrooms – 20-30 years
- Healthcare buildings – 20-30 years
- Retail units – 5-15 years
- Leisure buildings – 10-20 years
These lifespans assume periodic relocation. With continuous use in one place, they may endure significantly longer.
Temporary Buildings
For temporary modular buildings only expected to be needed for a short period, maximum lifespan is far lower.
Buildings used at construction sites or one-off events may only remain in place for 6-18 months. Structures used for emergency response, such as medical centres or shelters, may be rapidly deployed then repurposed after around 5 years.
The focus is on rapid installation and cost-effectiveness, not longevity. But they can easily be adapted, reused or recycled.
Comparison to Traditional Buildings
There is a common misconception that modular buildings have a shorter lifespan than those constructed traditionally on-site using materials like brick and mortar. But in reality, the expected life of both building types is similar.
When designed for long-term permanent use, modular buildings match or even exceed the lifespan of traditional construction, thanks to:
- Offsite prefabrication for quality control
- Precision manufacturing for consistency
- Ability to use proven durable materials
- Elimination of weather delays during construction
Any differential comes down to the materials and build quality – not the fact it is modular. With quality materials and regular maintenance, modular buildings offer equivalent longevity to traditional buildings.
Maximising Lifespan
There are certain steps that can be taken to ensure a modular building achieves maximum lifespan:
- Use durable, long-lasting construction materials
- Design for easy maintenance and repairs
- Create roof overhangs and covers to protect against rain
- Use sealed panels to minimise water damage
- Select paints/coatings to handle weathering and UV exposure
- Keep vegetation cleared around the structure
- Clean regularly to prevent build-up of grime
- Carry out strict quality checks during manufacturing
- Develop detailed maintenance plans for the life of the building
A well-designed and maintained modular building will still be going strong 60+ years down the track.
Conclusion
When delivered as part of a high-quality construction project using robust materials, modular buildings can offer exceptional longevity and performance on par with any traditional building.
Typical lifespan is a minimum of 60 years for permanent structures, with regular upkeep and maintenance required during this period. Shorter lifespan is expected for temporary or relocatable buildings.
Critical factors determining lifespan include the materials used, maintenance regimes in place and the quality of offsite construction techniques. By optimising for durability and resilience when designing and constructing the modular building, an equivalent or greater lifespan compared to conventional buildings can be readily achieved.