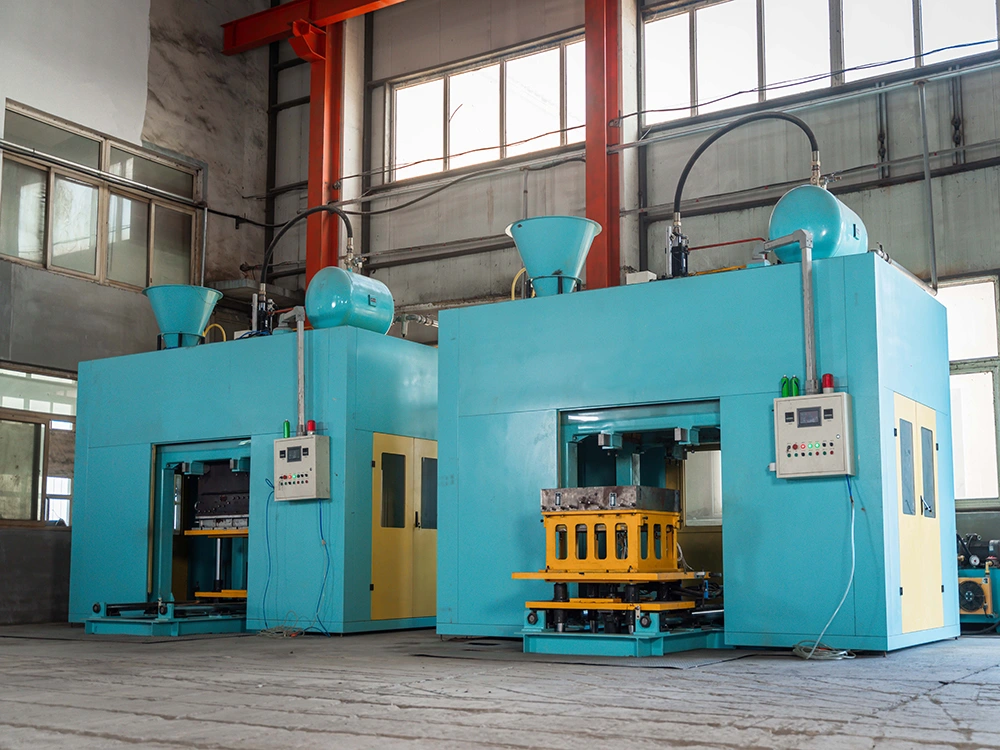
For ages, foundry technology has been a crucial component of manufacturing, allowing the creation of intricate metal components necessary for a variety of sectors.
As a result of the relentless pursuit of innovation, new procedures and approaches have been developed to improve the effectiveness, accuracy, and general casted quality.
Shell Mould Casting is one such invention that has attracted a great deal of interest. Many businesses favor this cutting-edge foundry technology because it has various benefits over conventional casting techniques.
This article will examine the nuances of Shell Mould Casting, as well as its benefits and the ways in which it is changing the face of foundry technology.
Understanding Shell Mould Casting
Shell model Casting is a precise casting method that makes the model out of a sand shell that is stuck together with glue. The process starts with making a pattern out of metal.
The design is then fired and covered with a refractory material to make it more resistant to heat. After that, this pattern is put into a two-part metal box. Resin-coated sand is then put between the pattern and the box.
Once the plastic hardens and the mold is free from the pattern, it is taken off, leaving a hole in the shape of the casting that will be made. The hole is then filled with liquid metal, which cools and hardens to make the finished product.
Advantages of Shell Mould CastingHigh Precision and Dimensional Accuracy
High precision and physical accuracy are possible when shell mold casting is used to make complicated forms. To make sure the end casting matches the design exactly, a shell mold is used. This means that very little post-processing is needed.
Fine Surface Finish
The smooth surface finish that Shell Mould Casting provides is one of its main benefits. The casting doesn’t need as many finishing steps because the smooth surface of the shell shape transfers to it. That makes the finished product smooth and nice to look at.
Reduced Machining Requirements
It is not necessary to do as much cutting when shell mold casting is used because the parts are so precise and have a smooth surface. This not only saves time but also cuts down on wasted materials, which makes the whole production process faster and cheaper.
Versatility in Material Selection
Shell Mold Casting can be used with many different types of materials, such as alloys and magnetic and non-ferrous metals. Because it is so flexible, makers can pick the best material for each job, making sure that the finished product works well and lasts a long time.
Improved Mechanical Properties
A fine-grained microstructure and better mechanical characteristics of the castings are produced by the controlled cooling procedure used in shell mould casting.
This process produces components that are stronger, harder, and more durable overall, making them appropriate for use in high-stakes applications in sectors like aerospace and automotive.
Cost-Effectiveness
Shell Mould Casting has benefits over conventional processes in terms of accuracy, decreased machining, and increased material use, which translate into long-term cost reductions despite higher initial setup costs. The total cost-effectiveness of this method is boosted by the minimum waste and decreased rejection rates.
Shorter Lead Times
Shell Mould Casting speeds up production processes because it doesn’t need as much cutting or post-processing. In today’s competitive market, shorter wait times are very important because they let producers react quickly to changing market trends and customer needs.
Applications of Shell Mould Casting
As a result of its benefits, Shell Mould Casting can be used in many situations and businesses:
Automotive Industry
In the car industry, Shell Mould Casting is often used to make engine parts, transmission parts, and other important parts that need to be very precise and last a long time.
Aerospace Industry
In the aircraft business, parts need to have great mechanical qualities and be exactly the right size. Shell Mold Casting is used to make aircraft parts, which guarantees the quality and dependability needed in this field.
Medical Equipment
When making medical tools, accuracy is very important. Shell Mold Casting is used to make parts for medical gadgets and tools that are very complicated and need to be very accurate.
Pump and Valve Manufacturing
A lot of the time, pump casings, impellers, and valve bodies need to have complicated forms and smooth surfaces. Because it meets these needs, Shell Mould Casting is the first choice for producers in this field.
Industrial Machinery
Shell Mould Casting’s high accuracy and minimal machining requirements are advantageous for a variety of parts used in industrial machinery, including gear housings and bearing supports.
Art and Sculptures
For painters and sculptors who need delicate and detailed castings for their works, shell mould casting is a popular option because of the exquisite surface quality it produces.
Conclusion
Foundry technology has led to better methods, such as Shell Mould Casting, that help manufacturers in many areas. This process is great for making high-quality metal parts because it is precise, accurate in terms of dimensions, has a great surface shine, and improves mechanical properties.
Shell Mold Casting is a symbol of how far businesses have come by increasing efficiency, lowering costs, and making better products as they grow and expect higher standards.
If this new technology is accepted and made better, it will change the way foundries work, leading to more advanced and efficient production.